Non UV Stable VS UV Stable Resin Bound Surfaces
- info515099
- Oct 9, 2024
- 2 min read
If you have had a non UV resin bound surface installed, you may have noticed that it has become patchy in areas where your car, a wheelie bin, or a plant pot has been placed for a short while. This is due to the two types of resin used for resin bound installations: UV stable resin (aliphatic) or non-UV stable resin (aromatic). It is crucial to ensure that your contractor is using UV resin to maintain a beautiful and consistent colour on your resin-bound surface.
Kamox strongly recommends the use of UVR stable resins for any applications
There are a number of reasons for this:
Non-UV stable resin can darken when exposed to sunlight – in as little as 2 weeks! In comparison, the effect of natural light on UV resin is reduced and even.
Shading may be inconsistent when using non-UV resin. If a customer parks a car, a wheelie bin, or even a plant pot on the surface, the areas covered by the object will darken over a short period of time, whereas other areas will maintain their original colour.
Non-UV is a very strong resin but sometimes it can become brittle and crack. UV systems (Aliphatic hardener) have a more flexible characteristic. This means the surface is less liable to cracking.
Non-UV resin is slightly cheaper than UV resin. However, it's important to consider the potential time and effort required to address an unhappy customer if your surface is affected. Once the sun exposure damage occurs, there is no way to fix it without resurfacing the entire surface.
Below are some examples (Image shows: The left side was laid using UV resin and the right side was laid using Non-UV. Pearl Quartz and Silver have significantly changed within only two weeks)
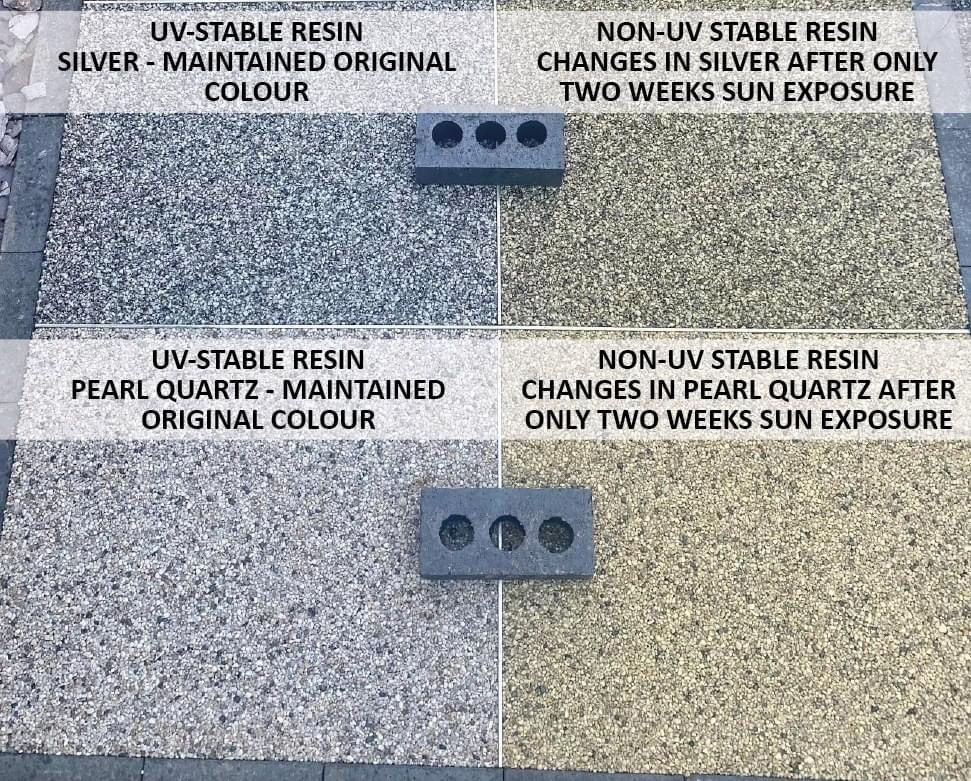